Breaking Barriers: How 3D Printing is Revolutionizing Mobility Aid Design
Lifestyle
2025-02-17 09:02:58Content
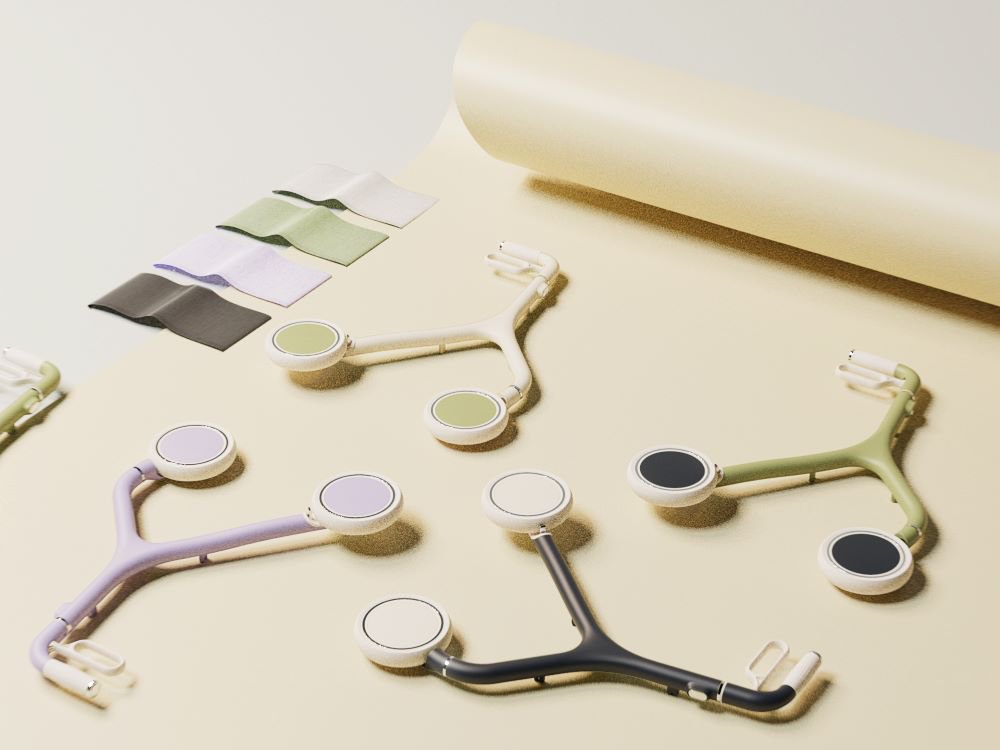
3D People played a pivotal role in supporting a sustainable lifestyle company's innovative product development journey. From the initial prototyping stages to the final finishing of plastic components, the team provided comprehensive technical expertise and precision manufacturing solutions.
The collaboration began with intricate prototyping, where 3D People's advanced techniques transformed conceptual designs into tangible plastic parts. Their specialized approach ensured each prototype met the company's exacting standards for quality and functionality.
A key highlight of their collaboration was the vapor smoothing process, which refined the plastic parts to achieve a superior surface finish. This technique not only enhanced the aesthetic appeal of the components but also improved their overall structural integrity.
By leveraging cutting-edge 3D printing technologies and meticulous finishing methods, 3D People enabled the sustainable lifestyle company to bring its vision to life with remarkable precision and efficiency. Their end-to-end support was instrumental in transforming innovative concepts into market-ready products.
Revolutionizing Mobility: How 3D Printing Transforms Sustainable Lifestyle Solutions
In the rapidly evolving world of technological innovation, the intersection of advanced manufacturing techniques and sustainable design has opened up unprecedented possibilities for creating transformative mobility solutions. The collaboration between cutting-edge 3D printing technologies and forward-thinking lifestyle companies represents a paradigm shift in how we approach product development and manufacturing.Precision Engineering Meets Sustainable Innovation: A Game-Changing Partnership
The Art of Advanced Prototyping
The journey of creating revolutionary mobility aids begins with an intricate dance of technological precision and creative problem-solving. 3D People emerged as a critical partner in this transformative process, bringing unparalleled expertise in advanced prototyping techniques. Their approach goes far beyond traditional manufacturing methods, leveraging state-of-the-art 3D printing technologies to reimagine how mobility aid components are conceptualized, designed, and produced. The prototyping phase represents a critical moment of innovation, where digital concepts transform into tangible, functional components. By utilizing advanced computational modeling and precision printing techniques, engineers can explore complex geometries and structural designs that were previously impossible with conventional manufacturing approaches. This method allows for unprecedented levels of customization and optimization, ensuring that each component meets exacting standards of performance and durability.Precision Plastic Part Manufacturing
Plastic component manufacturing has undergone a radical transformation with the advent of sophisticated 3D printing technologies. The process involves intricate layer-by-layer construction that enables unprecedented levels of detail and structural integrity. Each component is meticulously crafted, taking into account complex mechanical requirements and ergonomic considerations. The ability to produce lightweight yet robust plastic parts represents a significant breakthrough in mobility aid design. Traditional manufacturing methods often compromised between weight, strength, and complexity, but 3D printing eliminates these historical constraints. Engineers can now create components that are simultaneously lightweight, incredibly strong, and precisely tailored to specific functional requirements.Vapor Smoothing: The Final Touch of Refinement
Beyond initial fabrication, the vapor smoothing technique represents a sophisticated post-processing method that elevates the quality of 3D-printed components. This innovative process involves exposing printed parts to carefully controlled vapor environments, which chemically smooths surface irregularities and enhances overall aesthetic and functional qualities. The vapor smoothing technique provides multiple benefits beyond mere cosmetic improvements. It reduces surface porosity, increases material density, and can significantly improve the component's resistance to environmental factors. For mobility aids, this means creating parts that are not just visually appealing but also more durable and capable of withstanding rigorous daily use.Sustainable Design Principles in Action
The collaboration between 3D People and the sustainable lifestyle company exemplifies a holistic approach to product development. By integrating advanced manufacturing techniques with environmentally conscious design principles, they demonstrate how technology can drive meaningful innovation while minimizing ecological impact. Each stage of the manufacturing process is carefully considered through a sustainability lens. From material selection to production techniques, the goal remains consistent: creating high-performance mobility solutions that respect both human needs and environmental constraints. This approach represents more than just a manufacturing strategy—it's a comprehensive philosophy of responsible innovation.The Future of Mobility Aid Design
As technological capabilities continue to expand, the potential for transformative mobility solutions grows exponentially. The partnership between advanced 3D printing technologies and visionary design teams promises to unlock new frontiers of possibility, creating mobility aids that are not just functional tools but sophisticated, personalized extensions of individual human experience. The journey from conceptual design to finished product represents a remarkable testament to human ingenuity, technological prowess, and a commitment to improving lives through intelligent, compassionate engineering.RELATED NEWS
Lifestyle
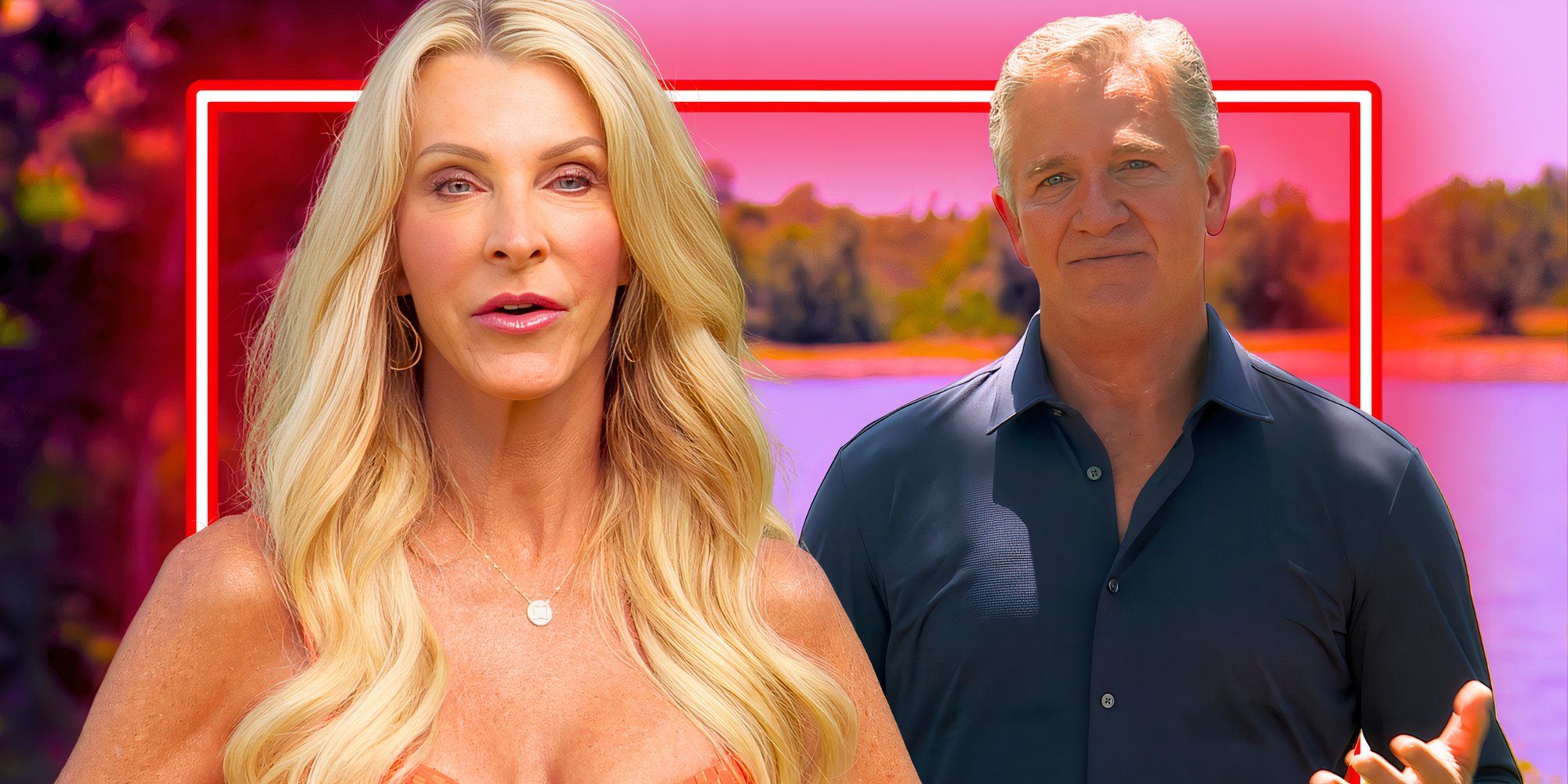
Love, Luxury, and Limits: Inside Joan and Chock's Lavish Bachelor Nation Escape
2025-02-10 12:00:19